In today's global world, more and more market-disruptive events will happen. There is no one-way solution to manage your supply chain agility and tackle all risks that could occur. Pick your key areas depending on your industry and strategy, and don’t overkill your risk management process.
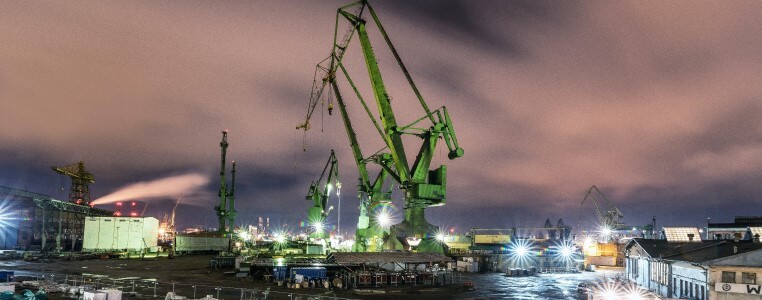
An unprecedented global drop in consumer spending
February 13, 2020, Chinese authorities shut down all non-essential companies including manufacturing plants in the Hubei Province. In the first quarter of 2020, some 460.000 Chinese companies closed down permanently because of the COVID-19 pandemic, causing an unprecedented global drop in consumer spending and the sharpest quarterly economic contraction ever recorded. A few months of limbo followed throughout the spring of 2020, with China rebounding already in Q2 and Q3 because of increasing global demand.
For some industries such as the car industry and tourism, recovery was slow and economic activity remained below pre-COVID levels. Other sectors like furniture and bicycle production saw a clear increase in demand compared to the pre-covid situation, with industries like pharma and sanitary goods even spiking.
Game-changers in Supply Chain management?
Another unforeseen disruption caused several supply chains to ‘dry up’ in the Spring of 2021. On March 23, the 400 meter long Ever Given carrying 18300 containers got stuck in the Suez Canal, blocking 12 percent of global trade. data According to Lloyd's List, the stranded ship was holding up an estimated $9.6bn of trade along the Suez Canal each day. The incident contributed to the global shortage of computer chips, the brain of any electronic device, and had an impact on many industries.
Save to say that COVID-19 and the Suez blockage will have contributed to 2020 and 2021 being a game-changing couple of years for Supply Chain Managers.
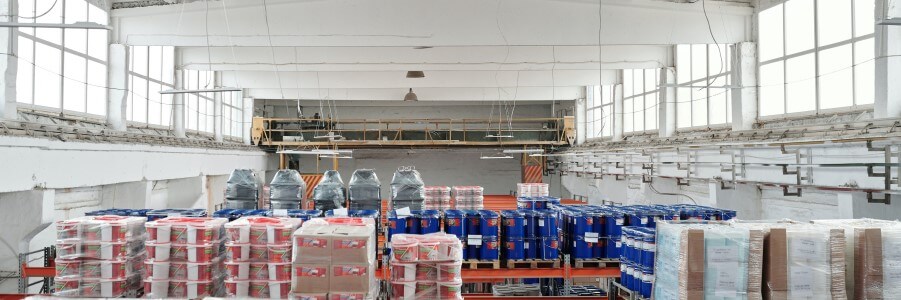
The problem with demand forecasting
Making sure Operations (sourcing, production, delivery, and return of goods) match the Sales commitment is a delicate exercise, managed in the Sales and Operations process.
Generally, it’s a series of monthly recurring meetings between different departments (Supply Chain, Sales & Marketing, Finance, Manufacturing & Operations, and product management), where the mid-to-long-term production plan is reviewed. The sales plan is reviewed against the available capacity, and decisions are made by senior management if there is a gap: sales numbers can be adjusted, or more commonly, the manufacturing capacity can be increased or decreased. In these turbulent times, a decision-making process that takes one month might be too long already.
Traditionally, in a Make To Stock environment (and depending on the company’s maturity), the demand forecast is calculated from historic demand and adjusted with market knowledge coming from the Sales department.
As historic data became worthless when the pandemic hit the world, this process became redundant for many companies.
Most industries, such as the car industry and tourism, had to significantly reduce their forecast for the first months, but the biggest challenge was to predict when and how the market would recover. Other industries, such as the retail sector were luckier to have a more stable (increased) demand, apart from certain products such as sanitary goods. Pharmaceuticals, and more specifically those companies that were developing a vaccine, had to plan for a huge peak in demand once they could bring their products to market. And who could foresee the increase in demand for furniture, generally a product bought in stores, now bought massively online?
Achieve end-to-end Supply Chain visibility of your goods, in real time, through efficient reporting to increase your decision speed instead of clinging to the traditional monthly S&OP process
Noëmie Colson, Supply Chain Project Consultant, CFO Services
How to improve supply chain agility for business continuity
To ensure business continuity, you need to think about your business agility and the agility of your whole supply chain.
- Create awareness across your organization, on every level, with clearly defined roles and responsibilities, and strong participation from top executives in your supply chain processes.
- Achieve end-to-end Supply Chain visibility of your goods, in real-time, through efficient reporting to increase your decision speed compared to the traditional monthly S&OP process.
- Increase the digitalization (IoT, AI - not only in manufacturing but also in demand & supply planning, robotics, warehouse automation..) of your supply chain to improve the decision-making process.
- Manage your customer expectations. Use market intelligence techniques, not only in marketing but also in your supply chain department.
- Set up a uniform supplier selection process analyzing potential risks and understanding the financial health of potential and existing suppliers.
- Optimize the relationship management with your suppliers and manage your contracts effectively to reduce supply risk.
- Analyze contract lifecycles to increase insights in suppliers that performed well and others that didn’t. Include clauses in your contracts that will help against potential risks, such as long term commitment of your suppliers, but allow flexibility and cost-sharing in case of unforeseen circumstances.
- Go from one single global to several local suppliers. Monitor not only your Tier 1 supplier but also companies further upstream your supply chain.
Depending on your companies’ supply chain strategy, there are many possibilities to improve its agility.
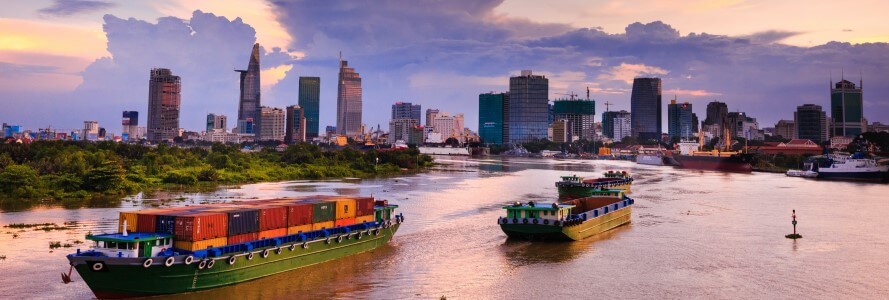
Cross-functional alignment through a mature S&OP process as a starting point
In the global world we live in today, more and more market-disruptive events will happen. There is no one-way solution to manage your supply chain agility and tackle all risks that could occur. Pick your key areas depending on your industry and strategy, and don’t overkill your risk management process. Cross-functional alignment through a mature S&OP process is a starting point. Cross-company -and even industry - alignment increases your whole supply chain agility. Communication is key.
Related content
-
Blog
Important: Fraudulent Whatsapp messages claiming to be from our company
-
Press release
TriFinance appoints Joost de Bruin as Group Managing Director
-
Event
EPM webinar: How CCH Tagetik can support your EPM journey
-
Article
Expanding Enterprise Performance Management across the company
-
Blog
What is Enterprise Performance Management (EPM)?
-
Blog
5 reasons why TriFinance is the perfect EPM partner for your organization